This type of variable valve works on some machines, but requires many precision adjustments to attain the wanted actuator control. In this condition, all flow is blocked through the valve. When the cylinder approaches the end of its stroke, a limit switch unloads the high-volume pump of the hi-lo circuit, decelerating the cylinder as quickly as friction on the machine members allows. by 24 volts at the amplifier. The enable voltage may range from 8.5-40 volts, although 10 volts is common. The valve includes an electronic control unit mounted into the valve housing or separately in an electrical cabinet. The actuator cannot run away with a throttle valve at this location. The Certified Fluid Power Specialists at Quality Hydraulics will assist you in selecting the best component, with the most efficient and cost effective solution. Because the cap end does not stay full, it will pause when it meets a load while the pump fills the cap-end void. Were always on the lookout for top talent. When the power supply is turned on and the enable signal is received, the on light will illuminate green. A computer, a PC, a programmable logic controller, or even a simple rheostat can produce the variable electric signal. If the load constantly changes, tapered cushions are only effective over a narrow range of the change. If the light stays on when plugged into the new valve, the problem is with the cable or connections. 2022 Endeavor Business Media, LLC. The circuit in Figure 14-20 shows an external pilot-operated pressure control valve teed into the cap-end line to provide a path for excess fluid to flow directly to tank. This is commonly referred to as onboard electronics (OBE). Systems that use proportional valves usually require a heat exchanger because energy waste is higher with this type circuit. The linear positioner moved 12 inches, Figure 6. When the power supply is turned on and the enable relay is not made, the LVDT will send approximately minus 12 volts back to the amplifier, signifying that the spool is in the fail safe position (Figure 3). Servo valves are used in conjunction with more sophisticated electronics and closed loop systems. It is not necessary to install the new valve for this test. It is essential that the oil entering the valve meet the standard set by the manufacturer. This arrangement eliminates some of the pressure spikes and reduces heat generation, but is more expensive. This arrangement gives twice rated flow without excess pressure drop or heat. Proportional valves are particularly suited to applications where the output pressure or flow is required to vary, either during a process or from one process to the next. https://www.linkedin.com/company/11091630, Volvo Sees Continued Growth Opportunity in Electrification, This Week in Power & Motion: Continental Building New Hydraulic Hose Factory in Mexico, Industry Provides Insight on Powering the Future of Electric Vehicles, Bosch Rexroth Launches Range of Electrification Products for Off-Highway Equipment, This Week in Power & Motion: igus Introduces Lubrication-Free Two-Component Ball Bearing, Poclain Makes New Investments to Accelerate Electromobility and Connectivity Development, Hydrogen-Battery Hybrid System Drives World's Largest Mine Haul Truck, Embark Trucks Advances Autonomous Driving Tech with Winter Testing and New Industry Partnership. To check these voltages, a multi-tester can be used by inserting the red and black leads into the appropriate connectors on the cable. The parallel flow path module comes with all flow paths internally drilled and sized to keep pressure drop to a minimum. In conclusion, by troubleshooting systems that utilize proportional valves, you can avoid lost production time as well as the unnecessary expense of sending off good valves for repair. The various speeds are achieved by changing the electrical signal level to deliver the flow/speed required. document.write(new Date().getFullYear()); If the actuator is a hydraulic motor or a double rod-end cylinder, volume at the inlet and outlet is the same. The LVDT centering adjustment should then be slowly rotated until the drifting stops. Inline filter low-pressure up to 100 bar, Inline filter medium-pressure up to 280 bar, Inline filters high-pressure up to 420 bar, Automatic back-flushing filter AutoFilt, Process filters in acc. When an on/off directional valve shifts, the cylinder free falls. Proportional valves have extremely tight tolerances between the spool and housing.

Direct-operated valves are smaller and less expensive than solenoid- pilot valves. The technological solution to these more complex circuits has been the development of proportional valves. To verify the power supply, insert the red lead into A and the black lead into B.. This position is commonly called the A position. Pressure, flow or another characteristic? To reduce energy waste, use a load-sensing pump and sense the line between the proportional valve and the directional valve. ** - Single Station Element, CETOP 5 - BM.5. With an over-running load at the cap end of the cylinder, the pump tries to force the cylinder to move faster than fluid can leave it. If these are reading correctly, the problem is most likely in the hydraulic system or the linear positioner. The valve spool in the fail safe position, Figure 4. Pilot operated valves are available in CETOP P05, ISO 4401-05, ISO 4401-07, ISO 4401-08 and ISO 4401-10 sizes.

Also use a throttle valve and a conventional directional valve to give smooth acceleration and deceleration of a cylinder to eliminate shock. The command voltage is input from the programmable logic controller (PLC) and determines the position of the valve spool. Dual flow paths shown in Figure 14-10 give twice the flow at the same pressure drop in either flow path. These valves are subplate mounted according to NFPA/T.3.5.1 R2-2002 and ISO 4401:2005 standards. Variable-volume, bi-directional pumps in closed-loop circuits give very smooth action, but are limited to operating a single actuator. Dependent on the type of proportional valve an electric, or pilot air, supply will be required, with appropriate control. Heavy loads at fast operating speeds usually require a means of acceleration and deceleration for smooth operation. Giving the extra oil a second path reduces rod-end pressure and wasted energy. Phone: (952) 895-6400

This is known as the fail safe position. Two types of integrated electronics are available, with analogue or fieldbus interfaces. Figure 14-8 depicts the symbol for a slip-in cartridge relief valve. EDF03M and EDF05M are direct operated normally closed proportional flow control valves with pressure compensation. When flows go above 150 to 200 gpm, use a slip-in cartridge relief valve with a direct-acting proportional relief pilot. The throttle valve configuration in Figure 14-10 gives infinitely variable flow. Load sensing also makes the circuit pressure compensated. Skol Marketing. Load sensing lets the system operate at lower pressures during most of the cycle.

As the proportional valve shifts to move the actuator, restricted flow from the opposite side controls acceleration, deceleration, and maximum speed. Tel:+39 0522 505811 The various models are available with or without on-board electronic (OBE), feedback and in closed loop as well as Fieldbus and IO-Link configurations. Electromobility: HYDAC opts for technology-neutral solutions. When the cylinder slows to the speed of the low-volume pump, it continues to the end of stroke at a velocity low enough to eliminate most of the shock. The command voltage will then drop to zero, and the proportional valve spool will once again shift into the electrically closed position. Once the enable relay is closed, a current signal will be sent to the solenoid. Wind Power: filter elements in after-sales, Oil cleaning on lifting platforms with FAPC 016, Return filter series E 454-156 VD with diffuser, Tank-mounted return filter E 451-156 with AirEX air separation, Tank-mounted return filter kits RFI 206 / 406, Digitalization in Mass Production: Online Condition Monitoring, High-pressure safety filter series HD 040/081/150. These revolutionary valves allow infinite positioning of spools, thus providing infinitely adjustable flow volumes.

This rapid, full shift can cause an actuator to jump or lunge on start up and produce excessive shock when stopping. Fluid Power Division Secondary speed is adjustable to meet any requirement. Other options include valves with specially designed flow controls and spool-stroke adjusters set for a specific machine function. Feedback sensors are necessary for the valve to control any particular process, for example, pressure and temperature mentioned above. A throttle valve has internal leakage and may not be able to prevent cylinder drift. The symbol for the solenoid indicates that the valve operates off a variable electrical signal. As the cylinder moves, the linear-displacement transducer sends an analog or digital signal back to the PLC. A proportional control valve system can be used to improve control of most machines without the high price tag of servo control systems.Quality Hydraulics & Pneumatics, Inc. offers design, products and systems for all three types: directional, proportional and servo valve control systems. Usually, varying shifting time of the spool controls acceleration and deceleration. One way to control acceleration in these circuits is to shift a standard open-center solenoid valve to extend the cylinder and let excess pump flow relieve to tank during acceleration. They are dependable, cost-effective and give fast response and consistent control. Use proportional control valves to reduce shock and give a finer degree of control to circuits that do not require extreme position accuracy, or repeatable speed and force. For the best experience on our site, be sure to turn on Javascript in your browser. Continental Hydraulics J Series On-Board proportional valves with Spool Position Feedback are offered both in Direct Operated NFPA D03 (NG6) and NFPA D05 (NG10) as well as Pilot Operated Proportional Directional Control Valves. Figures 14-6 and 14-7 show symbols for infinitely variable pressure-relief and reducing valves. For the best experience on our site, be sure to turn on Javascript in your browser. Fx: (847) 680-5325
The oil should be sampled regularly to ensure the system meets this standard. ** - Single Station Element, CETOP 2 - BM.2. The easiest way to determine where the failure is occurring is to remove the LVDT cable from the existing valve and plug it into a new valve. Electronic signals to these circuits also can vary the speed of the actuators infinitely. A command voltage of 6 volts is input into the amplifier. Regulated acceleration and deceleration result in improved machine overall cycle times and production rates. Email:reception.fp@dana.com, I accept the privacy terms and conditions, Tech Data Proportional Directional Valves, Tech Data Proportional flow control valves, Tech Data Proportional pressure control valves, Axial piston pumps - Variable displacement - Closed loop, Axial piston pumps - Variable displ. The three numbers correspond to the 4-, 6- and 14-micron particles in a 1-milliliter sample taken from the system. The power supply is typically 24 volts and is used to power the amplifier. If no input enable voltage is present, the wiring and output signal should be checked from the PLC. The flow control variety of valve generally selects an orifice which only allows a specified volume of flow to pass. If the power supply drops below 21 volts, the red UB light will come on.
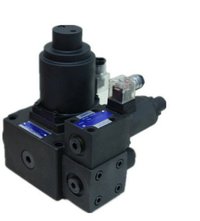
(In this application, a cylinder with standard cushions will eliminate virtually all shock.). The excess fluid retards the cylinders motion. While the design of proportional directional valves may vary from one manufacturer to another, they all essentially perform the same function: controlling the direction and speed of a hydraulic cylinder or motor. Consider that the magnet is attached to a spool in a valve, the pressure or flow can be controlled in proportion to the current applied to the solenoid. These cookies are used to collect information about how you interact with our website and allow us to remember you. ** - Single Station Element, CETOP 3 - BM.3. 3D CAD models can be found in the product tree at the according products. Another option for decelerating a load is to specify a cylinder with longer than standard cushions that have a tapered flow cutoff. The increased current causes the valve spool to shift until the LVDT feeds back minus 6 volts. Want to start the conversation? Air may need to be supplied at a given quality, requiring the correct filtration. The cleanliness level is determined by the ISO 4406 code for the specific valve. One throttle valve in the main pump line can vary the speed to one actuator or several that cycle at different times.

If the cylinder must set without creep, use a counterbalance valve. We aim to help our customers get the most out of their products, enabling them to drive down the total cost of ownership. Many are programmable, with onboard diagnostics, making them highly suited to Industry 4.0 system design. A proportional valve may have feedback control, but the response time of the valve is too slow to get the precise control that a servovalve circuit provides. Two problems can occur when using a standard spool-type proportional valve with single-rod-end cylinders and running-away loads. To reduce speed change, add a feedback signal from the actuator (similar to a servovalve circuit). The store will not work correctly in the case when cookies are disabled. This circuit is good for resistive loads only because it meters fluid to the cylinder. (Some manufacturers offer proportional valves with spools that only allow approximately half flow through the rod port. Continental Hydraulics offer Both Direct Operated NFPA D03 (NG6) and NFPA D05 (NG10) as well as Pilot Operated Proportional Directional Control Valves. Soft-shift solenoids with variable flow controls offer more range and give better control for some circuits. The valve can then be driven with the boxs drive adjustment. This offers a variety of machine cycles, safely operated at greater speeds, yet with controlled start and stop characteristics. When there is no power to the valve coil, the spring will shift the spool to the position shown on the far left. Actuator feedback will help but is still not extremely accurate because most proportional valves do not respond quickly enough to overcome sudden system changes. A shuttle valve provides pressure feedback from each cylinder port to the reducing valves remote-control port. ** - Multi Station Subplates, Special Subplate With Automatic Exclusion Regenerating Circuit, Pressure Control Valves (In Line Mounting), Flow diverters and 2 way cartridge valves ISO 7368 (Logic Element), 2 way cartridge valves ISO 7368 (Logic Element), Proportional directional control valve 4/3, 4/2, direct operated, Open Loop, Proportional directional control valve 4/3, 4/2, direct operated, Close Loop with electrical position monitor LVDT. Fax: (952) 895-6444 The cost of a proportional valve can be as much as 50 percent of the cost of a servo valve of the same size. Via Giulio Natta 1, 42124 Reggio Emilia Italy As a result, servo valves are always much more expensive.

The command voltage comes into the amplifier via the D and E pins. However, solenoid-pilot proportional valves can handle higher flows some in excess of 200 gpm.

In some cases, the enable signal is not used. ** - Multi Station Subplates, CETOP 5 - BS.5. If the linear positioner is drifting, the LVDT may not be in the proper position. Waukegan, IL 60085
To null the valve, the LVDT access cover should be removed. The symbol in Figure 14-9 shows the valve piped for a single flow path. Varying voltage to the coil limits spool travel to control the maximum speed of an actuator. Figure 14-19 shows the cylinder running away from the pump, causing cavitation in the cylinders cap end. Continental Hydraulics offers a complete range of proportional valves: pressure control, flow control, directional, explosion-proof, high response. Figure 14-15 shows another shock-free deceleration circuit. This is usually 0-10 volts or in some cases 4-20 milliamps. - Open and closed loop, Axial piston motors - Variable displ. To check the command voltage from the PLC, insert the red lead into D and the black lead into E. A 0-10 volt signal should be shown depending on the command signal from the PLC. Rotate the zero adjustment until the linear positioner stops drifting or oscillating. A horizontally mounted cylinder typically requires force at all times to stroke. Use a proportional control card with adjustable ramps for this application. The volume difference is almost 50% when using a 2:1 rod cylinder.

An LVDT adds cost to the valve and the electronics, but is usually necessary in all but simple acceleration/deceleration circuits. To find out more about the cookies we use, see our, DISTRIBUTOR LOGIN - STOCK CHECK & PRICING, Directional Control without On-Board Control, Directional Control with On-Board Control, Pneumatic Hydraulic Manually Operated, High frequency response and fast Step Response, Din and Deutsch coil connection available, On-Board microprocessor controls all the valve function, LVDT for high performance and repeatability, Certified for ATEX, IECEx and INMETRO options, A low temperature version (up to 40 C) is also available, Provides remote control over pressure in a pilot circuit to 130 GPM and pressures to 5000 PSI, Available with or without On-Board Electronic controls, Open loop and closed loop for Position, Force and Velocity applications. The third type of hydraulic directional control technology is the servo valve. Figure 14-14 shows the circuit with a closed-center valve and a pressure-compensated pump. In this example, if the valve has a maximum flow rating of 10 GPM, then 6 gallons per minute will flow through the spool when shifted with a command voltage of 6 volts. Pressure scales stabilize the pressure drop in proportional directional control valves to ensure the independent control of the load. The schematic diagram in Figure 14-13 shows a double pump in a hi-lo circuit that operates this way. The pressure compensator is a reducing valve that has a fixed spring setting (say 150 psi). If the light flickers as the machine operates, this normally indicates loose connections. A simple proportional valve depends on solenoid force working against a spring to position the spool. If speed or positioning problems are occurring, the command and LVDT signals should be checked at the appropriate connections on the amplifier. An accumulator in the circuit enhances cycle response time and protects the pump from pressure spikes. Without an external drain, pressure at the outlet of the counterbalance valve adds to the spring setting that keeps the valve from opening. Use a PC or PLC to produce the variable signal to change pressure any time the machine sequence requires it. The Duplomatic Group designs and manufactures technology solutions for motion control in multiple sectors. Proportional directional valves control inlet and outlet flow so that there is pressure at both ends of an actuator when it moves.